Power Plant Pipe Composite Replacement
Power Plant Pipe Replacement
Projects
- Steel Tank Rehabilitation
- Pipe Replacement
- PCCP Repair
Project Highlights
- River headworks structure warming water pipe completely corroded
- Customer evaluated traditional replacement – determined that it would require a multiyear timeframe
- Pipe is submerged during high river level, complicating the repair process
- Unique solution was developed to build a composite replacement pipe using the existing pipe as a form
- Qualified the replacement as a capital project
The Problem
The 2,400 megawatt coal-fired power plant operates a warm-water discharge pipe in the Missouri River at the intake structure. This prevents ice buildup on trash racks and warms water entering the condenser during cold weather.
The pipe is approximately 165′ in length, ranges in diameter from 6′-6′ at the center to 4′ at each end, and is fed from the plant circle water system.
After the original installation, the plant added a 24″ discharge line on the upstream side of the warming line to push river debris off the trash racks. The piping has outlet holes on the bottom where warmed water is discharged into the river.
The pipe is typically fully immersed in the river but when river levels are low can be fully exposed. Over its service life, the pipe has suffered significant corrosion both externally and internally. While particularly bad at welds, the entire pipe had lost substantial wall thickness and many weld areas were corroded completely through. The largest gap was between the warming line and the discharge pipe, where 37″ of steel was completely corroded away.
The plant planned to replace the pipe with either carbon or stainless steel in the same configuration and solicited bids for this work. In discussing unrelated work, we suggested the plant consider using carbon fiber in lieu of steel replacement. While there was interest in this approach, there were concerns about whether a carbon fiber solution was viable, and more importantly, whether it could be considered replacement and thus capitalized.
The Fix
Working with engineering partners, a carbon fiber design was developed that used the remaining host pipe as a mold for a full replacement value carbon fiber composite pipe. The new pipe was designed to take all internal and external loading of the original carbon steel pipe. This design included transitioning from an internal replacement in the warm-water pipe to an external replacement of the discharge line without relying on the remaining host pipe for any structural capacity.
Because of schedule and capital spending issues, the plant awarded the contract in late November and needed the project finished by December 31. The design work was completed in 5 days, during which the site was mobilized. The installation work then began in early December.
As the project progressed, temperature forecasts indicated river temperature dipping below 36 degrees F before the new pipe was scheduled to be completed. At that temperature, the possibility of “trickle ice” forming in the river and blocking the intake was possible, potentially shutting down all four units. The project schedule was thus accelerated at the plant’s request, despite working in below freezing temperatures for the duration of the project.
The work was completed eight days ahead of schedule, just before river temperature dipped below 36 degrees, at which point the plant put the new composite warming line into service.
The Result
Despite the highly accelerated schedule, weather issues, and multiple safety complications related to open water, confined space, use of accelerants, and large-scale heaters, the entire work scope was completed in four weeks with a perfect safety record and within budget.
Advantages of composite solution:
- Much shorter schedule
- Lower plant impact
- Lower cost
- Construction materials are not subject to corrosion, providing a longer life-cycle with little or no maintenance
- Engineered and backed by both code and design guidelines, and comes with PE Stamped Drawings
- The CFRP solution is “green”: there is no demolition involved and the construction materials (carbon fiber) are actually byproducts of oil refining
- The system requires no heavy equipment or floating plant for installation and does not require separate pipe spools between spans
- The CFRP system minimizes or eliminates underwater construction, lowering costs and minimizing risk
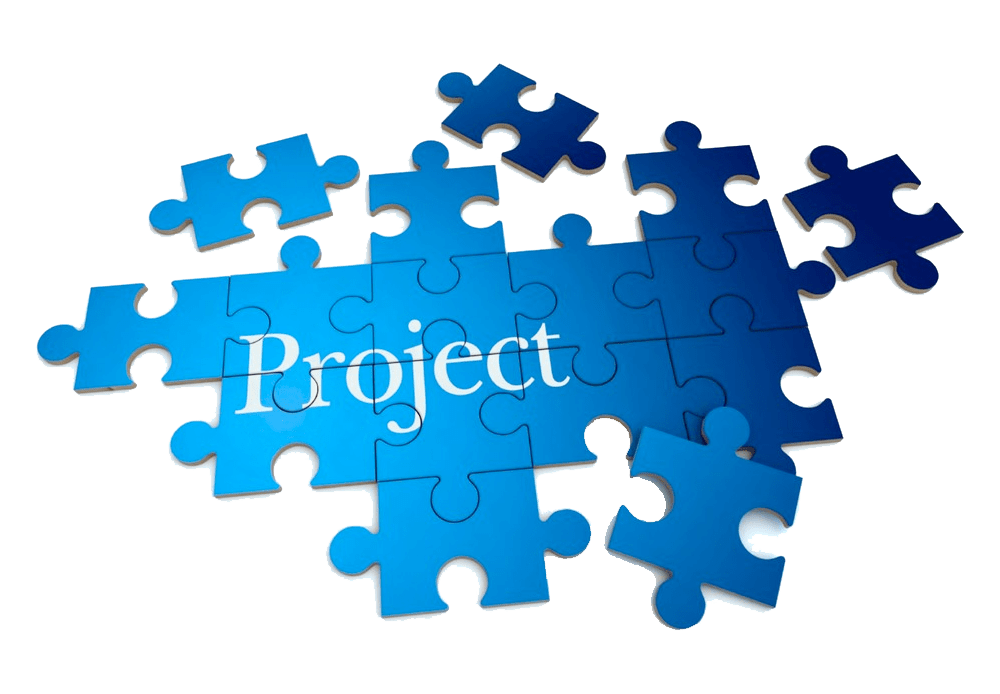